Kun puhutaan juotoshelmistä, meidän on ensin määritettävä tarkasti SMT-vika.Tinahelmi löytyy reflow-hitsatusta levystä, ja voit yhdellä silmäyksellä todeta, että se on suuri tinapallo, joka on upotettu virtausaltaaseen, joka on sijoitettu erillisten komponenttien viereen, joilla on erittäin alhainen maankorkeus, kuten levyvastukset ja kondensaattorit, ohuet pienet profiilipaketit (TSOP), pieniprofiiliset transistorit (SOT), D-PAK-transistorit ja vastuskokoonpanot.Tinahelmiä kutsutaan usein "satelliiteiksi" niiden aseman vuoksi suhteessa näihin komponentteihin.
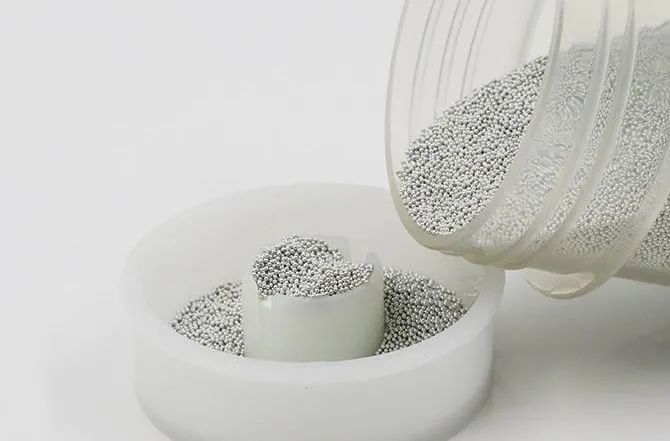
Tinahelmet eivät vaikuta pelkästään tuotteen ulkonäköön, vaan mikä tärkeintä, painetun levyn komponenttien tiheyden vuoksi on olemassa vaara, että linjassa syntyy oikosulku käytön aikana, mikä vaikuttaa elektronisten tuotteiden laatuun.Tinahelmien valmistukseen on monia syitä, jotka johtuvat usein yhdestä tai useammasta tekijästä, joten meidän on tehtävä hyvää työtä ennaltaehkäisyssä ja parantamisessa, jotta voimme hallita sitä paremmin.Seuraavassa artikkelissa käsitellään tekijöitä, jotka vaikuttavat tinahelmien tuotantoon, ja vastatoimia tinahelmien tuotannon vähentämiseksi.
Miksi tinahelmiä syntyy?
Yksinkertaisesti sanottuna tinahelmet yhdistetään yleensä liialliseen juotospastan kerrostumiseen, koska siitä puuttuu "runko" ja se puristuu erillisten komponenttien alle muodostaen tinahelmiä, ja niiden ulkonäön lisääntyminen johtuu huuhtelun käytön lisääntymisestä. - juotospastassa.Kun lastuelementti asennetaan huuhdeltavaan juotospastaan, juotospasta puristuu todennäköisemmin komponentin alle.Kun kerrostunutta juotospastaa on liikaa, se on helppo puristaa.
Tärkeimmät tinahelmien tuotantoon vaikuttavat tekijät ovat:
(1) Mallin avaaminen ja alustan graafinen suunnittelu
(2) Mallin puhdistus
(3) Koneen toistotarkkuus
(4) Reflow-uunin lämpötilakäyrä
(5) Paine
(6) juotospastan määrä astian ulkopuolella
(7) Tinan laskeutumiskorkeus
(8) Haihtuvien aineiden kaasun vapautuminen linjalevyssä ja juotosvastuskerroksessa
(9) Liittyy virtaukseen
Tapoja estää tinahelmien muodostuminen:
(1) Valitse sopiva alustagrafiikka ja koko.Varsinaisessa tyynyn suunnittelussa se tulisi yhdistää PC: n kanssa ja sitten todellisen komponentin pakkauskoon mukaan, hitsauspään koon mukaan suunnitella vastaava tyynyn koko.
(2) Kiinnitä huomiota teräsverkon tuotantoon.On tarpeen säätää aukon kokoa PCBA-levyn tietyn komponenttiasettelun mukaan juotospastan tulostusmäärän hallitsemiseksi.
(3) On suositeltavaa, että paljaat PCB-levyt, joissa on BGA, QFN ja levyssä tiheät jalkakomponentit, suorittavat tiukkoja paistotoimia.Varmistaaksesi, että juotoslevyn pinnan kosteus poistetaan hitsattavuuden maksimoimiseksi.
(4) Paranna mallien puhdistuksen laatua.Jos puhdistus ei ole puhdasta.Mallin aukon pohjalle jäänyt juotospasta kerääntyy lähelle mallin aukkoa ja muodostaa liikaa juotospastaa aiheuttaen tinahelmiä
(5) Varmistetaan laitteiden toistettavuus.Kun juotospasta tulostetaan, mallin ja tyynyn välisen siirtymän vuoksi, jos siirtymä on liian suuri, juotospasta imeytyy tyynyn ulkopuolelle ja tinahelmet ilmestyvät helposti lämmityksen jälkeen.
(6) Ohjaa asennuskoneen asennuspainetta.Riippumatta siitä, onko paineensäätötila kiinnitetty tai komponentin paksuuden säätö, asetuksia on säädettävä tinahelmien estämiseksi.
(7)Optimoi lämpötilakäyrä.Säädä reflow-hitsauksen lämpötilaa, jotta liuotin voi haihtua paremmalla alustalla.
Älä katso "satelliitti" on pieni, ei voi vetää, vedä koko keho.Elektroniikassa paholainen on usein yksityiskohdissa.Siksi prosessituotannon henkilöstön huomion lisäksi asianomaisten osastojen tulee myös toimia aktiivisesti yhteistyössä ja kommunikoida prosessihenkilöstön kanssa ajoissa materiaalimuutoksista, vaihdoista ja muista asioista, jotta materiaalimuutosten aiheuttamat prosessiparametrien muutokset estetään.Piirilevypiirien suunnittelusta vastaavan suunnittelijan tulee myös kommunikoida prosessihenkilöstön kanssa, viitata prosessihenkilöstön antamiin ongelmiin tai ehdotuksiin ja parantaa niitä mahdollisuuksien mukaan.
Postitusaika: 09.01.2024